Unlocking Success: Casting Aluminum Made Easy
Unlocking Success: Casting Aluminum Made Easy
Blog Article
Aluminum Spreading Providers Revealed: Vital Insights and Tips
Exploring the realm of light weight aluminum casting solutions can unveil a globe of intricate procedures and nuanced considerations that are crucial for effective results. As markets progressively transform to aluminum for its light-weight yet resilient properties, recognizing the fundamentals of casting comes to be critical. From the basic techniques to the intricate details that can make or damage a casting task, there is a wide range of understandings and pointers waiting to be uncovered. As we venture right into the world of aluminum casting solutions, prepare to uncover the crucial elements that can form the trajectory of your jobs and boost your understanding of this elaborate craft.
The Essentials of Aluminum Casting
What essential processes are entailed in light weight aluminum spreading that create the foundation of this commonly used production strategy? Aluminum casting is a versatile and cost-efficient method made use of in different industries to develop complicated and elaborate metal parts.
Secret elements such as mold and mildew style, gating system, and cooling price play an essential duty in figuring out the last top quality of the actors light weight aluminum component. The mold can be made of numerous materials like sand, investment, or steel casting wax, depending upon the ins and out of the component and the preferred surface area coating. After solidification, the mold is eliminated, and the casting undergoes ending up procedures such as warm machining, surface, and treatment layer to satisfy the required specifications. Recognizing these fundamental processes is crucial for accomplishing high-quality aluminum spreadings with precise measurements and mechanical residential properties.
Various Casting Approaches Discussed
Checking out the different methods utilized in aluminum casting uses useful insights into the diverse techniques utilized to achieve precise and intricate metal components. One common approach is sand spreading, where a mold is created making use of compacted sand around a pattern of the preferred component. This technique is economical and versatile, ideal for both simple and complex shapes. Another approach, die casting, entails injecting molten aluminum right into a steel mold under high stress. Die casting enables high precision and repeatability, making it ideal for mass manufacturing of little to medium-sized parts. For even more complex layouts, financial investment spreading is frequently chosen. This method makes use of wax patterns that are melted away, leaving a tooth cavity for the molten light weight aluminum to fill. Financial investment casting returns exact details and smooth coatings, making it popular in markets such as aerospace and vehicle. Each spreading technique has its unique advantages and is selected based upon factors such as complexity, price, and volume factors to consider.
Aspects to Consider When Choosing a Service Provider
When choosing a light weight aluminum casting service supplier, evaluating their experience and expertise is important for guaranteeing quality and dependability in the manufacturing process. The supplier's experience in the field suggests their experience with different casting methods, potential obstacles, and ideal techniques. It is crucial to ask about the kinds of projects they have functioned on in the past, ensuring they line up with the intricacy and specs of your own task.
Furthermore, think about the supplier's online reputation within the industry. Look for testimonials, endorsements, and study that show their capability to provide premium aluminum spreadings regularly. A reputable copyright will typically have certifications or associations with industry companies, showcasing their commitment to quality and adherence to industry criteria.
Additionally, analyze the company's capacities in terms of modification, volume needs, and project timelines. Ensure that they can accommodate your certain needs and have the versatility to range production as needed. Reliable communication and openness concerning expenses, lead times, and quality assurance processes are likewise critical elements to take into consideration sites when selecting a light weight aluminum spreading provider.

Typical Difficulties and Solutions
Navigating through the intricacies of light weight aluminum casting procedures usually offers makers with a collection of obstacles that need innovative solutions to make certain effectiveness and high quality in production. One common obstacle dealt with in aluminum spreading is the development of problems such as porosity, contraction, or incorporations because of improper mold design or poor steel high quality. These defects can endanger the structural stability of the end product. To resolve this, makers should carry out detailed simulations and tests to enhance the spreading process criteria and ensure the top quality of the molds and products used.
One more difficulty depends on attaining exact dimensional precision, especially for intricate geometries. Variations in cooling rates, mold growth, and product residential properties can result in inconsistencies from the desired dimensions. Applying advanced innovations like computer-aided design (CAD) and computer system numerical control (CNC) machining can boost accuracy and consistency in aluminum casting. Furthermore, keeping appropriate control over the melting and pouring procedures is crucial to stop problems like overheating or unequal distribution of the molten metal - casting aluminum. By purchasing automation and real-time monitoring systems, producers can improve procedure control and decrease variations, inevitably boosting the total high quality of aluminum cast items.
Tips for Optimizing Your Casting Projects
By guaranteeing that the gating system is well-designed and effectively positioned, you can improve the circulation of molten aluminum and minimize the chances of defects in the final casting. Furthermore, using computer system simulations can help in anticipating and examining the circulation of metal during the spreading procedure, allowing for changes to be made before actual production starts.
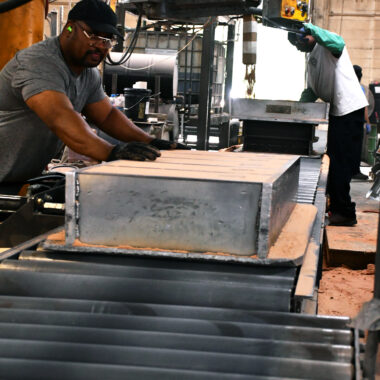
Conclusion
To conclude, understanding the fundamentals of light weight aluminum spreading, different spreading approaches, elements to take into consideration when choosing a service provider, usual challenges and options, and pointers for optimizing casting tasks are important for successful end results. By sticking to these insights and executing finest techniques, individuals and companies can guarantee reliable and reliable light weight aluminum spreading solutions that satisfy their details needs and requirements.
Understanding these fundamental processes is important for click here to find out more accomplishing premium light weight aluminum spreadings with specific measurements and mechanical residential or commercial properties.
When choosing an aluminum casting solution provider, assessing their experience and know-how is vital for making sure high quality and integrity in the production process. Reliable communication and openness relating to expenses, lead times, and high quality control procedures are additionally essential elements to take into consideration when choosing an aluminum casting service copyright.
Navigating via the intricacies of light weight aluminum casting YOURURL.com processes usually offers makers with a collection of difficulties that call for ingenious services to make certain effectiveness and high quality in production. One common obstacle dealt with in light weight aluminum spreading is the formation of defects such as porosity, contraction, or additions due to inappropriate mold style or inadequate steel quality.
Report this page